SpaceTech Deployment Mechanisms for Space Solar Arrays & other Subsystems
SpaceTech develops selected satellite equipment, both, for use in our solar arrays and in other subsystems, making extensive use of our in-house manufacturing and test capabilties. We have a thorough understanding of details of satellite equipment and "hands-on" experience in development,
manufacturing, assembly, integration and test, being an ideal foundation for the development of higher levels of integration as in subsystems.
SpaceTech mechanisms – Products and projects
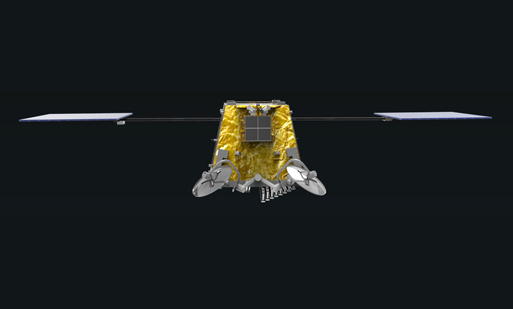
The AOS Airbus OneWeb Satellites mega constellation for global broadband internet consists of 618 small satellites. AOS selected SpaceTech to develop and deliver 1800 solar arrays deployment mechanisms SADM. Delivering key parts to make this project a success, SpaceTech proves its suitability for the New Space Market as a flexible and cost-efficient SME.
SpaceTech SADM development
SpaceTech’s AOS SADMs consist of a CRFP booms and SAP launch support parts.
The booms are equipped with two tape spring hinges and the harness for the solar array and the seasonal drive. The CFRP boom with integrated high strength alloy tape springs is manufactured by CarboSpaceTech and provides a high stiffness in deployed configuration. The power harness is directly attached to the boom and provides high performance due to its low resistance.
Safe launch suspension is achieved by one release mechanism that pretensions the solar array panel and the boom.

Kompsat-3 is an optical earth observation satellite built by the Korean Aerospace Institute (KARI), which was finally launched in 2012.
The Kompsat-3 solar array deployment mechanism (SADM) was the first flight hardware contract for SpaceTech, signed 2005/2006 with Korean Airlines Ltd. The contract also included the delivery of stiffening mechanisms for each of the solar arrays, to achieve a high eigenfrequency of the solar array wings in order to allow for agile satellite operation/pointing.
SpaceTech SADM key features
- Very low friction
- High torque margin
- At the same time low deployment shock through a cam/spring driven system
Links
Learn more about KOMPSAT-3A (Korea Multi-Purpose Satellite-3A) / Arirang-3A
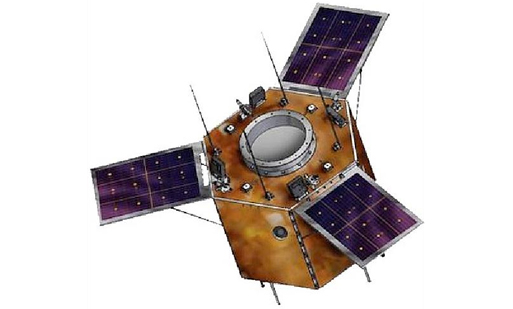
The SpaceTech solar array deployment mechanisms for GökTürk-2 is based on the flight proven SpaceTech design as flown on KompSat-3 and used earlier on Globalstar and Champ mission for their deployable booms.
In stowed configuration each solar panel is resting on four supports held by one central Hold-Down and Release Mechanism (HDRM). A thermal knife release mechanism was selected for shock free release.
Links
Learn more about GökTürk-2

The RIME Antenna (Radar for Icy Moons Exploration), SpaceTech's contribution to the ESA JUICE (JUpiter ICy moons Explorer) mission, is an instrument which will investigate the geophysical structure of Jupiter's three largest icy moons – Europa, Ganymede and Callisto.
Goal of Jupiter's icy moons mission
It will begin its journey to Jupiter in 2022, arriving there in 2029. Scientific goal of this mission is to search for liquid water below the ice sheets which cover the surfaces of the moons. Liquid water is considered the basis of life in the universe. preservation of a spacecraft is the number one priority. Essential AOCS input needs to be provided by high reliable sensors.
Key characteristics of the SpaceTech JUICE RIME antenna
- Total mass of less than 7 kg for the whole antenna and less than 2 kg for the antenna booms made of ultra-light CFRP for a total deployed length of 16 meters, allowing savings in propellant on the long flight to Jupiter
- Release mechanism lightweight non-explosive actuators
- Integrated elastic hinge technology with multiple foldings (6 hinges) is used. When deployed these hinges ensure extreme high stiffness and alignment performance over the wide temperature range necessary to fly-by Venus and then operate in cryogenic cold environment in the backyard of the moons of Jupiter. The elastic hinge is achieved by cutting slots into the CFRP tube, resulting in an extremely light weight all CRFP hinge without any metallic bracket or blades.
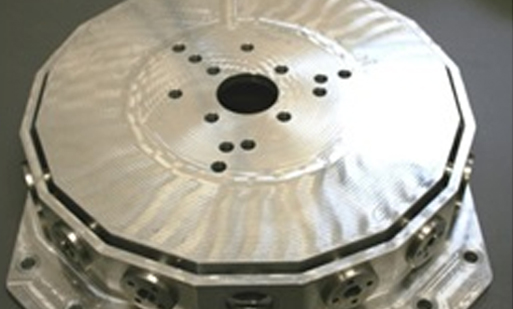
SpaceTech developed a modular damping system for satellite reaction wheels. Minimizations of two factors were intended:
- The transmitted vibrations of the reaction wheel to the satellite
- The transmitted vibrations of the satellite to the momentum wheel
SpaceTech Reaction Wheel Damper design
A damping system prototype with adjustable characterization for both cases was designed and produced.
The system and interfaces can be adapted to any reaction wheel, S/C interface and mission.
The test component shows an excellent functional performance for vibrations from the satellite to the reaction wheel and in opposite direction.
Key features of the STI Reaction Wheel Damper
- Very significant damping of micro-vibrations during space mission
- Very significant protection against launch loads, particularly at higher frequencies
- Adjust natural frequencies for launch (high loads) and in orbit (low loads) fairly independent thanks to load dependent stiffness (random and shock environment will not any more cause degradation of ball bearing quality of the reaction wheels)
- Adjust performance to mission needs
- No launch lock necessary
SpaceTech Reaction Wheel Damper benefits
- Reduced loads for existing wheel to avoid pre-damage of flight ball bearings before flight
- Better compliance to micro vibration requirements especially for high frequencies
Find more details about SpaceTech deployment mechanisms:
Download our brochure on deployment mechanisms